The Shed 107, March/April 2023
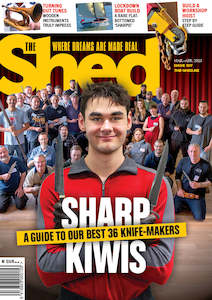
Cutting edge
In New Zealand, knife-making is increasing in popularity year by year. If the recent Auckland Blade Show was anything to go by, this pastime is now a full-time career for a large number of sheddies and of enormous interest to the general public. The hundreds who came through the doors over the two-day event are evidence of knife-making’s huge growth over these past few years.
Who are these knife-makers; what separates and what inspires them? Where are they, and what knives and blades do they create?
We’ll soon know more because in this issue of The Shed we profile 36 of NZ’s finest. Read our Who’s Who and Where’s Where in this issue in an extensive rundown of our 36 best Kiwi knife-makers.
“The art of shaping blades is more than a utilitarian act; it is something of a primal impulse, one that predates our relocation from the cave.
Without some form of cutting edge, our ancestors would have struggled to hunt, fish, gather food, build homes, or even defend themselves. Down through the ages, we have used everything, from quartz, flint, pounamu, and obsidian to copper, bronze, iron, and titanium. Today, a worldwide profusion of cutlers, sheddies, and blacksmiths is once again heeding that ancient call: to perfect a version of our most important tool, the knife.
Those who are doing the forging, beating, and grinding in New Zealand are as diverse as the blade and handle shapes they produce. There are teachers and nurses; chefs, lawyers, and engineers; and some who are not yet tertiary students. One thing all makers, suppliers, and even knife importers have in common is their passion for the art and craft of knife-making, coupled with a collective sense of support that they get from being a part of the wider community."
Kiwi ingenuity
After the comprehensively damaged Christchurch central city was sealed off after the 2011 earthquake — causing most of the city’s eating houses to close down — Neville Watkinson could see that his restaurant furniture business was doomed. Before the sale of his premises was completed, he started building a Milford 20 in the loft above the joinery workshop’s office, despite the obvious limitations of the space.
“ Neville wanted to build a ‘sharpie’ — a shallow-draught sailing boat — and was impressed by the design of the sharpie ketch, Floridays , from the drawing board of well-known US designer Mark Fitzgerald, which he had seen on the internet.
Neville contacted Mark, who said that he didn’t have comprehensive plans for the boat, as he had the only example, which he still owns, built 30 years before under his direct supervision."
Alibre 101 — part four
In this, part four of the series, we are shown how to take advantage of some of the clever features of the Alibre Atom3D software.
“In this issue , we will be creating a vee pulley using mirroring and patterning tools. This takes your skills another step forward as we learn how to use more of the handy tools available in the Alibre Atom 3D program. In part three, we learnt how to produce a 2D drawing from the 3D model we had created of the 17mm deep socket, so, after completing this vee-pulley design, you might like to produce a drawing of it, too.
Start by opening the Alibre Atom program and looking at the home page. Click on the New Part icon. You can determine what each icon represents by moving the cursor over it; some text will appear stating what that particular icon does.
The workspace will open up with a ribbon toolbar across the top of the page and the Design Explorer table down the left side."
Make a workshop hoist
Des Bromilow is a very, very busy sheddie but is finding that these days moving heavy objects around the workshop is not as easy as it once was. Sheddie solution? Find an affordable and effective way to make a device to do the heavy lifting for you.
“ The problem I am trying to solve: getting older and weaker. Since I don’t have a solution for the problem, I figure I can try to work smarter by designing and building something to reduce the impacts of the problem.
One impact is the challenge of lifting heavy things, such as chucks onto the spindle of the lathe or a vice or universal dividing head onto the table of a milling machine. "
Music makers
Two Waikato men have turned their love of music into works of art in wood. Laurence Frangos-Rhodes is a young guitar maker and Menzshed member Keith Day thought he’d have a go at making a bugle out of wood!
“ Looking for something to fill all his new spare time, Keith discovered the city’s Men’s Shed, a group of mostly woodworking enthusiasts shoehorned into a room in what had been the city’s electricity de